What is 3D printing?
3D printing is a process of making a three-dimensional solid object of virtually any shape from a digital model. The three-dimensional model is created by adding successive layers of melted material on top of each other. Each layer is a horizontal cross section of the 3D model, so when each cross section is placed on top the one directly underneath, the model is created.3D printing is considered an additive process, since melted material is added. This is the opposite of subtractive manufacturing, in which material is removed from a mold to create a 3D object.
How do 3D printers work?
Before you can start 3D printing, you need to create a model that your 3D printers can read and interpret. To do this, you must use 3D software. Tinkercad is recommended for beginners, and Fusion 360 is the most popular 3D software for both hobbyists and professionals.Once you have finished creating your 3D model in CAD (Computer Aided Design) software, you must export your 3D model as a printable file, such as .STL (stencil file) or .OBJ (object file). Your 3D printer cannot directly read this file, so you have to perform a process called slicing. Slicing is the process of converting your 3D model into a series of instructions that your 3D printer can understand. This is done by using a slicer, which is a software that converts your 3D model into a series of instructions that your 3D printer can understand. During slicing, the software converts your 3D model into thousands of layers that dictate the position of the 3D printer's nozzle, which is essential for the 3D print to come out correctly. Ultimaker Cura is the most popular slicer for 3D printers and it exports the slice as a .GCODE (Go Code) file.
Types of 3D printing
Vat Photopolymerization
Vat Photopolymerization is a type of 3D printer which has a container filled with photopolymer resin. The build platform, or the platform on which the 3D model will be built, is partially submerged inside the vat of resin, with only a small layer of resin above the build plate. A UV light shines on the area of the resin that needs to be hardened to form a layer, and once the first layer is finished, the build plate is lowered and the next layer is hardened. This process continues until the 3D object is finished, at which point the 3D model is removed from the vat of resin.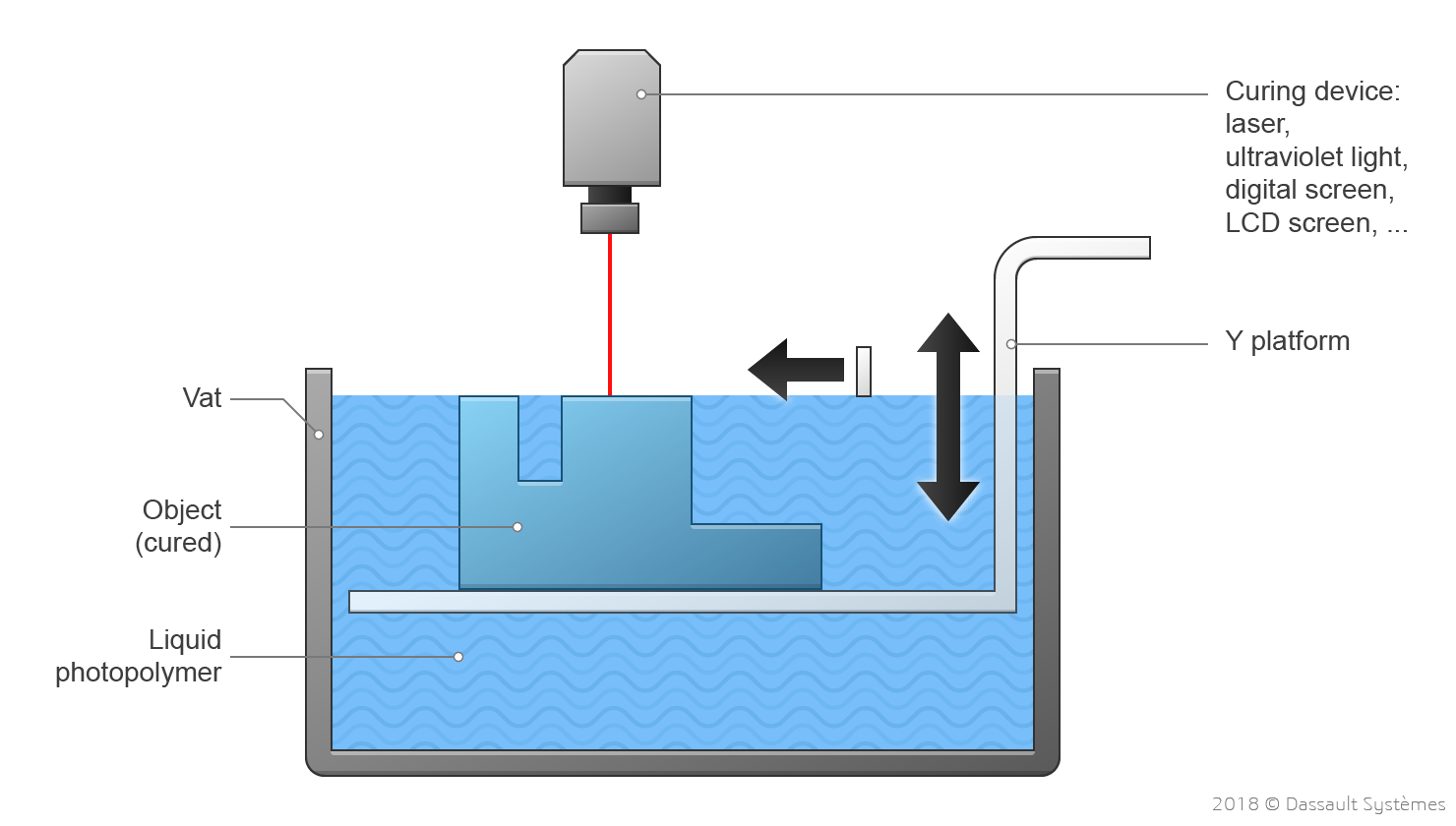
The source of UV light varies in different methods:
- Stereolithography (SLA) was invented by Charles Hull, the founder of 3D Systems, in 1986. In his method, the UV light comes from a laser precisely controlled by rotating mirrors. The method has high precision and high build quality.
- Direct Light Processing (DLP) is similar to SLA, but it uses UV projectors instead of lasers. These UV projectors are controlled by micromirrors, which arrange themselves so that an entire layer has light shining on it at the same time. Since the light is not controlled precisely, but entire layers are created immediately, there is a much higher print speed at the expense of resolution and build quality.
- LCD Shadow Masking (mSLA) is a relatively new method of 3D printing and has a variety of names, such as 'Direct UV Printing' and 'mSLA'. In this method, a LCD screen blocks off the area of UV light that doesn't need to be shined onto the vat of liquid photopolymer. Essentially, the LCD screen replaces the bulk, expensive UV projectors in DLP, but it comes at a cost. The LCD screen wears out over time and must be replaced much more often than DLP projectors. LCD printing provides the advantage of quick printing and a more affordable 3D printer, but just like DLP, it has low resolution and low build quality.
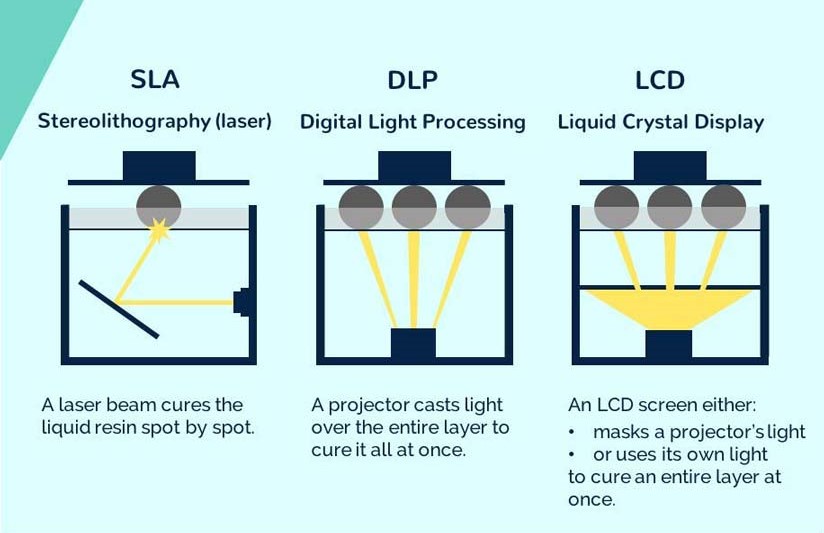
Material Jetting
Material jetting printers are the printers I see the most at schools and libraries. In material jetting, build and support material are pushed through a nozzle and deposited onto the build platform, where it is then hardened by UV light. The build platform is then lowered and the next layer is deposited. This process continues until the 3D object is finished, at which point the 3D model is removed from the build platform.
Binder Jetting
Binder jetting involves two materials: powder base material and a liquid binder. The powder base material is spread in equal layers and the liquid binder is sprayed onto the powder base material. The liquid binder hardens the powder base and the excess powder is removed from the plate and stored for use in the next 3D printing project. Binder Jetting was invented at MIT in 1993.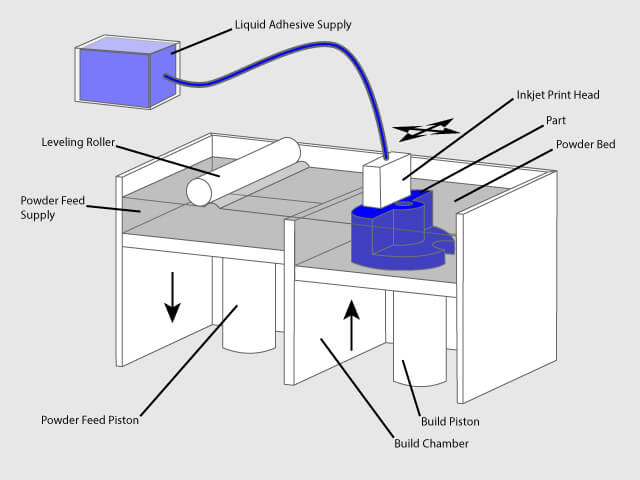
Material Extrusion
There are two main types of material extrusion printers: fused deposition modeling printers and fused filament fabrication printers, but both types are essentially the same.Fused Deposition Modeling (FDM)
FDM printers use a plastic filament as material. As the plastic filament moves through the printer's nozzle, the heated nozzle melts the filament. The building plate moves in the x, y, and z directions while the nozzle stays in place. Since the material hardens immediately upon leaving the printer's nozzle, FDM is an efficient printing process.FDM was invented by Scott Crump, the founder of Stratasys, in the late 80's. FDM has been patented by Stratasys.
Fused Filament Fabrication (FFF)
Fused Filament Fabrication is another term used to refer to FDM printers. Members of the RepRap project coined the term to circumvent the legal restrictions on using the term FDM when selling printers of this type.Good luck and happy printing!